挟まれ事故・巻き込まれ事故を防ぐ方法!事故事例をあわせて解説
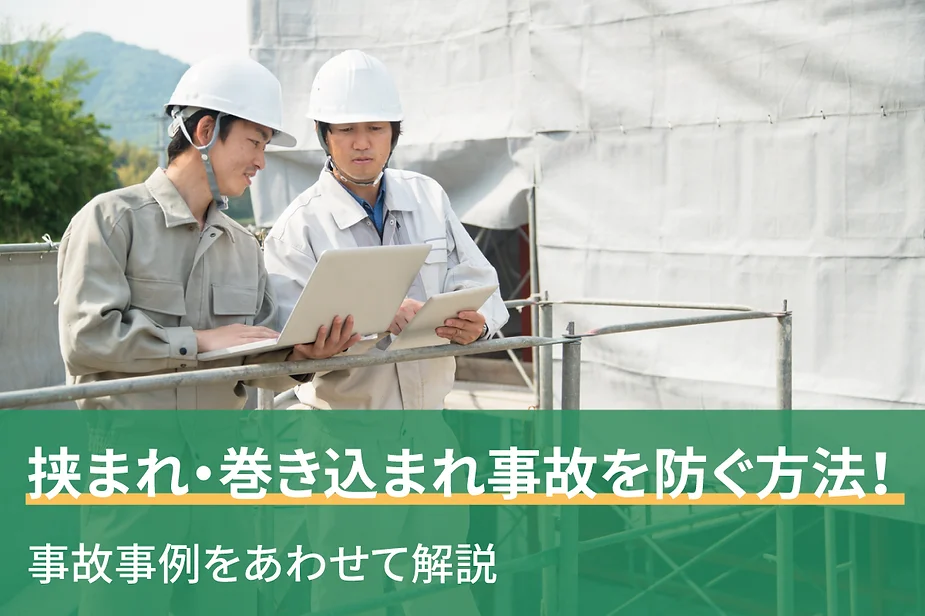
挟まれ事故や巻き込まれ事故は、作業現場で起こりやすい事故で死亡するリスクも高いです。しかし、実際に事故に遭遇したことのない人の中には、そのリスクに実感が持てないという方もいるでしょう。そこで、事故の発生状況や事例、対応策を紹介します。
挟まれ事故・巻き込まれ事故は、作業現場で起こりやすい事故で死亡するリスクも高いです。実際に、そういった事故に遭遇したことはないものの、起こりうる可能性があれば、知識を持っておきたいとお考えではありませんか。
この記事では、挟まれ事故・巻き込まれ事故の発生状況や具体的事例、防止するための対応策について紹介します。この記事を読むことで、事故防止のためにどのような点に気を付けるべきかが理解でき、事故を未然に防ぐことができます。

挟まれ事故・巻き込まれ事故の発生状況
中央労働災害防止協会・安全衛生情報センターの資料によれば、2008年に死傷した人の内、挟まれ事故・巻き込まれ事故の割合は14.3%を占め、第3位になっています。ちなみに第1位は転倒で19.2%、第2位は墜落・転落の17.4%でした。挟まれ事故・巻き込まれ事故(死傷)の産業別の発生割合を見ると、1位が製造業(54.3%)、2位が建設業(11.5%)、3位が運輸・交通業(10.3%)と続いています。
1位の製造業だけで見ると、挟まれ事故・巻き込まれ事故は死傷者の29.0%を占め、第1位ですが、これは第2位の転倒(15.3%)の2倍近くに及んでいます。さらに、死亡事故に限定して見ていくと、製造業で死亡した人の31.9%が挟まれ事故・巻き込まれ事故の犠牲となっており、2位の墜落・転落(15.4%)の2倍近くです。
以上から、挟まれ事故・巻き込まれ事故は、労働災害の中でも発生する可能性の高い事故で、死亡につながるリスクも高いということがわかるでしょう。ここからは、さらに詳細な発生状況について見ていくことにします。
挟まれ事故・巻き込まれ事故の起因物
挟まれ事故・巻き込まれ事故には、必ず起因物があります。この起因物を把握することが、事故発生のリスクを回避するうえでは重要です。起因物の中でも、特に大きなボリュームを占めるのが動力機械です。
2008年の挟まれ事故・巻き込まれ事故(全産業)の起因物の割合を見ると、第1位が一般動力機械(24.2%)、2位が動力運搬機(18.2%)、3位が金属加工用機械(12.6%)でした。これら3種類の割合を合計すると55%になり、半数以上を占めていることがわかります。
ちなみに、2007年の挟まれ・巻き込まれによる死亡事故(製造業)で見ていくと、1位が一般動力機械(35.8%)、2位が金属加工用機械(23.6%)、3位が動力運搬機(13.2%)で、合計で72.6%です。 これに4位の動力クレーン等(5.8%)、7位の木材加工用機械(3.2%)を加えると81.6%になります。材料やそのほかの機械・工具による事故もあるものの、事故の多くは動力機械によって起きていることがわかります。
挟まれ・巻き込まれ部位は手が多い
労働者健康安全機構によると、挟まれ・巻き込まれ部位として最も多いのは手であると報告されています。指・手・腕が巻き込まれ部位の60%を占めており、中でも指が多いことが指摘されているとのことです。
手の挟まれ・巻き込まれ事故が多い原因として、手には確実な保護具が存在していないことが挙げられています。足の挟まれ・巻き込まれについては、安全靴が普及したことで減少してきているとのことですが、手に関してはこのような保護具はありません。
また手については、つい無意識に動かしてしまいがちな点も挙げられるでしょう。特に何も考えずに、うっかり機械のうえに手を乗せてしまい、挟まれ・巻き込まれ事故が起きてしまうこともあります。
以上から、挟まれ・巻き込まれ部位として多いのは手で、手による事故の防止に努めなくてはならないことがわかります。
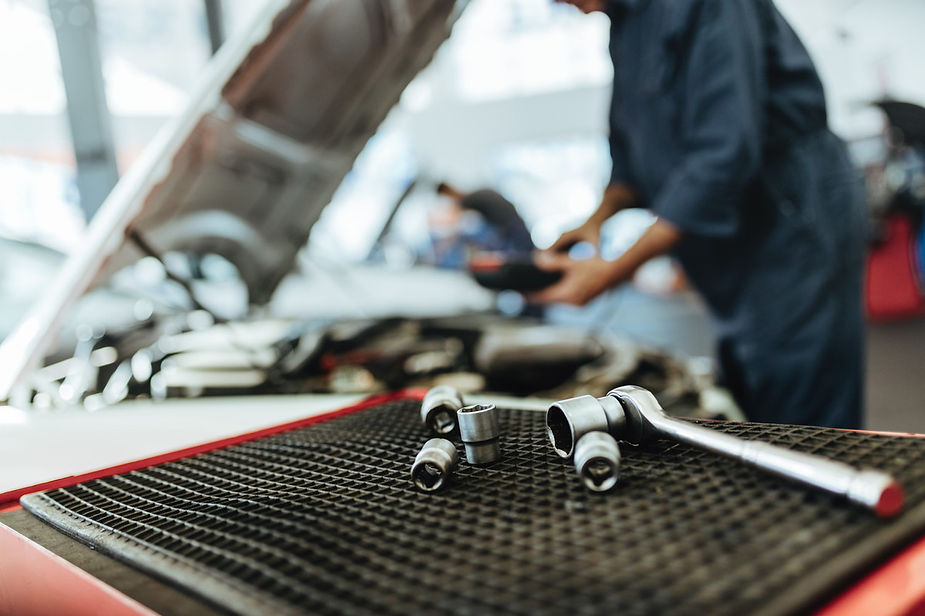
挟まれ事故・巻き込まれ事故の原因
挟まれ事故・巻き込まれ事故にはさまざまな原因がありますが、労働者健康安全機構による報告では、下記の原因が代表例として挙げられています。
- 機械運転中に手を出してしまった
- 安全装置が不十分だった
- 非定型作業のため、作業標準が作られていなかった
- 作業についてのルールが守られていなかった
- 危険予知が不十分だった
- 設計に安全が組み込まれていなかった など
機械を運転している最中に、ついうっかり手を出して事故が起きてしまうケースでは、危険に対する知識が不足していた、技能が未熟だった、自己過信や手抜きといった意欲欠如、人間特性(うっかりした、ぼんやりしたなど)などの原因が考えられます。
安全装置の不十分については、人がほとんど近寄らない機械のため、安全性に配慮せずにカバーが取り付けられていない、隙間など寸法上の問題などで、可動式ガードがインターロックになっていないといった不備が見られるようです。
また、安全装置はあっても人を適切に検知できなかったり、緊急停止ボタンが離れたところに設置されていて、いざというときに手が届かなかったりしたケースもあるようです。
ほかにも作業標準が作られていない、作業ルールが守られていない、危険予知が不十分だった、設計に安全が組み込まれていなかったなどのことも相互に関係しながら、挾まれ事故・巻き込まれ事故を引き起こす要因になっています。
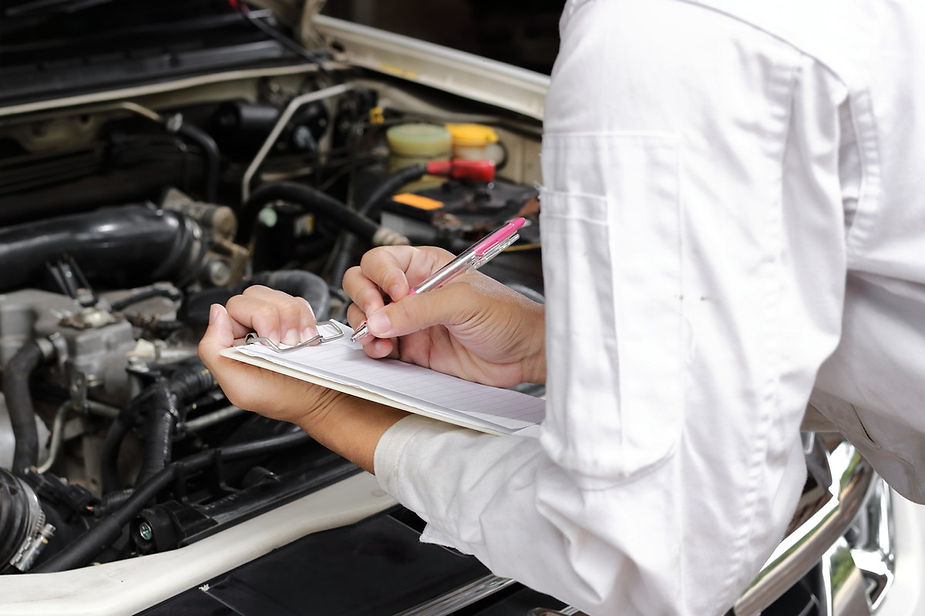
挟まれ事故・巻き込まれ事故を防止する対策方法
挟まれ事故・巻き込まれ事故を防止するためには、下記のような対策が必要だと考えられています。
- 機械設備の安全性を向上させる
- 安全対策を徹底させる
- 作業環境を整備する
- 作業を適正化し、安全教育を行う
それぞれについて、以下で詳しく解説します。
機械設備の安全性を向上させる
挟まれ事故・巻き込まれ事故は、機械設備の安全性の不備から起こることも多いです。そのため、機械設備の安全性は常に高く保たなくてはなりませんが、安全装置がきちんと動作し、万が一誤動作をした場合の安全策が講じられている機械の導入が必要です。
また、危険な作業については、自動化できないかどうかも検討の余地があるでしょう。もちろん、機械設備が安全であっても、事故発生のリスクはゼロとはいえません。
機械を使った安全な作業手順を明確に定め、現場の責任者から作業員に周知徹底する必要があります。また、決められた作業手順に従って、作業員が安全に作業しているかどうか、責任者は定期的に巡回して確認するようにしたほうがよいでしょう。
安全対策を徹底させる
作業を開始する前には、機械装置・安全装置、それから付帯装置も含め、安全点検を逐一行うようにしましょう。点検項目に抜けがあると危険なので、点検項目のリストを用意し、必ずリストにチェックして行うようにすべきです。
続いて、機械装置のメンテナンス(清掃・点検・修理)時は、機械の運転を必ず止めましょう。起動装置は施錠し、「メンテナンス中」の表示板を置くなどして、誰かが誤って起動できないようにします。メンテナンス中の事故も多いので、注意が必要です。
このほか、機械に特に異常が見えられない場合でも、年に1回は専門業者に点検を依頼し、その履歴を記録していきましょう。機械の周囲や施設の要所要所に注意喚起の掲示などをして、作業員の注意を促すことも必要です。さらに、械に衣料が巻き込まれることもあるので、作業着の正しい着こなし方なども徹底すべきでしょう。
このほか、機械の周囲に立ち入り禁止エリアを作る、防護ネットを設置するなど、できる限りの対策をあらかじめ講じておくとよいでしょう。タバコを投げ捨てる行為も事故を誘発する危険があるので、喫煙場所など喫煙のルールを厳しく決めておく必要があります。
作業環境を整備する
作業環境を見直して、必要に応じて整備することも大切です。普段当たり前のように使っている作業場ですが、冷静に眺めてみると改善の余地があるかもしれません。作業に不要なものがあれば取り除き、通路や作業スペースは広めに確保するとよいでしょう。
また、作業場を一度整理したとしても、その状態を維持しなくては意味がありません。4S(整理・整頓・清潔・清掃)の徹底、責任者による定期的な巡回などを行い、常に安全な環境が保たれるようにしましょう。
作業を適正化し、安全教育を行う
機械設備や環境面での安全性が確保できたら、今度は作業員の動きについても安全性を高めなくてはなりません。そのために必要なのが、作業の適正化と安全教育です。全ての作業員が正しい作業手順に則って、安全に作業できるように責任者から周知徹底する必要があります。
特に、新たに加わった作業員や、作業内容および機械設備に変更があった際などには、慎重に教育を行わなくてはなりません。非常に危険度が高い作業や有害な作業については、ほかの作業とは別に、特別な指導を行うべきです。
また消化器の使用方法など、非常時の訓練も常に行わなくてはなりません。作業をする前には作業員全員で作業の危険予知をする、作業中に集中力を切らさないために、突然声をかけたりしないようにすることも、徹底すべきです。点検・確認を常に意識して、チェックシートの活用や指さし呼称なども定着させていきましょう。
安全意識を身につけるためには、安全教育コンテンツを配信する「ZIKOZERO(ジコゼロ)」の活用も効果的です。ZIKOZEROは、実際に過去に起きた労災事故をリアルなCGで再現することで、作業員の危険意識を高めます。
コンテンツは、パソコンやスマートフォンなどからいつでもどこでも視聴できます。認知心理学者監修によって動画が作成されており、作業初心者やベテラン・安全管理者など、対象別のコンテンツがあることが特徴です。
現場での安全教育に加えて、このようなツールを導入することで、事故リスクをさらに下げることができるでしょう。

挟まれ事故・巻き込まれ事故の5つの事例
ここからは、過去に実際に起きた「挟まれ事故・巻き込まれ事故」を見ていきましょう。ただし、ここで紹介する事故はほんの一例に過ぎないため、これらの事例から、原因や対策について考えを深めて、未知なるリスクに備えていきましょう。
フォークリフトとトラックに挟まれて死亡
雨天のため屋内作業場にて、作業員の1人がトラックに荷物を積むために、荷台の扉を開けていました。その近くでは、別の作業員がフォークリフトで荷物を移動させていました。フォークリフトを運転していた作業員は、トラックについては視認できていたものの、もう1人の作業員の存在については確認できていませんでした。
その状態で、フォークリフトを運転している作業員が、フォークリフトを後退させてしまったため、トラックの荷台の側にいたもう1人の作業員は、フォークリフトとトラックに挟まれて死亡してしまいました。その作業場には、フォークリフトの誘導員は配置されていませんでした。
事故の原因
- 誘導員を配置することなく、作業員をフォークリフトの近くに立ち入らせてしまっていた
- フォークリフトやトラックでの作業について、運行経路を含めた作業計画が定められていなかった
- 同じ場所で作業を行う作業員同士が、連絡や調整を行っていなかった
- 雨天のため屋内作業場で作業が行われていたが、屋内は狭いので、フォークリフトと作業員の距離が近くなっていた
- 安全衛生委員会で、フォークリフトについての「ヒヤリハット・事故事例」が報告されていた。それにもかかわらず、立ち入り禁止措置や誘導員の導入などが検討されていなかった
対策
- 立ち入り禁止区域を設定し、歩行者と車両の経路を明確に分ける。フォークリフトの危険範囲には作業員を立ち入りさせない。やむを得ず立ち入りさせる場合には必ず誘導員を配置する
- トラックやフォークリフトについては、必ず運行経路を含めた作業計画を定める
- 作業員間での連絡・調整を行う
- 屋内作業場の範囲を広げ、フォークリフトと作業員の距離が近くならないようにする
- 安全衛生委員会の活動を活発化させる。ヒヤリハットや事故事例について、適切な安全対策を検討させる
クレーンとパレットの間に挟まれて死亡
ある作業員が、熱処理済みの鋳鉄ピストンを移し替える作業をしていました。作業員は、格段に35個のピストンが乗っているパレット(上段にはダミーピストンが35個、下段にはダミーピストンが1個と製品が34個乗っていた)の上段からダミーピストンを2個取り、そこにチェーンスリングのクランプをかけ、クレーンで吊り上げようとしました。
その結果、クレーンの支柱が倒れ、作業員はクレーンとパレットの間に挟まれて死亡しました。通常、製品やダミーピストンを置いた状態でパレットをクレーンで吊り上げることはありません。パレットとダミーピストンの総重量は、クレーンの定格荷量を超えていました。
事故の原因
- 吊り上げる荷の重さを確認しないまま、クレーンの定格荷量を超える荷を吊り上げた
- 作業手順書が作られておらず、作業員がそれぞれ自己判断で作業していた
- 作業員に対して、クレーン作業についての安全教育がなされていなかった
対策
- クレーンの定格荷量を超える荷を吊り上げない
- クレーン作業について、リスクアセスメントを実施し、クレーンの転倒防止策を盛り込んだ作業手順書を作成して、作業員に周知する
- クレーンでの作業について、定期的に安全教育を行う
外国人作業員がプレス機で手首切断
経験1カ月の外国人作業員が、パソコンデスク昇降部レールの曲げ作業中、プレス機内部に手を差し込んだ状態で機動ペダルを踏んでしまいました。その結果、プレス機が作動して右手首が切断されてしまいました。
事故の原因
- 右手を差し込んだ状態でプレス機を動作させたこと
- プレス機に手を入れてはいけないという教育はなされていたはずだが、経験が浅く、つい手を入れてしまった
- 経験が1カ月しかなく、安全作業手順が未習熟だった
対策
- 作業ゾーンに手を入れた場合に、設備を停止するインターロック機構を設置する
- 教育などのソフト面だけでなく、ハード面での対策が必要
回転中のローラーに手が巻き込まれた
作業員が、ゴム形成用のロール機の清掃をしていました。別の作業員が、ロール機の停止スイッチを押したのを確認し、ローラー上部のゴム寄せに付着したゴムを取り除こうと手を伸ばしました。その結果、惰性で回転していたローラーに手が巻き込まれ、手の指が切断されてしまいました。
事故の原因
- ローラーに手が挟まれないようにするための安全カバーや安全柵がなかった
- ローラーの回転が完全に止まったことを確認せずに、回転部分に手を入れてしまった
- 急停止装置を使用せずに、通常の停止スイッチを押して停止させたため、清掃作業中も惰性でローラーが動いてしまっていた
- 安全教育が不十分だった
対策
- ローラーの隙間に安全カバーや安全柵を取り付ける
- 危険箇所に体の一部もしくは全部を入れる場合、機械が完全に停止したのを確認してからにする。また
- 不意に機械が動かないように注意する
- 清掃などを行う際には、急停止装置を使用するように作業手順を変更する
- ヒューマンエラーに留意した、フェイルセーフな仕組みを構築する。非定常作業を含めて安全な作業標準を作成し、作業員に周知する
エレベーターのカウンターウェイトに挟まれて死亡
作業者は補助者の2人と一緒に、エレベーターの搬器の上に乗って点検作業を行っていました。搬器の上にいた作業員は、入口側から吹き抜け側に移動し、搬器の上の機器の点検を始めました。この点検作業がほぼ終わる頃、作業員は隣のエレベーターに面するフィルターをはずそうとしました。その途中、隣接するエレベーターのカウンターウェイトと、ガイドレール支持枠の水平材との間に、右足を引きずり込まれてしまいました。
事故の原因
- 隣接するエレベーターが運転状態だった
- 不自然な姿勢を強いられるような位置に、クーラーが設置されていた
- 作業の標準化が不十分だった
- エレベーターの点検作業における、挟まれ事故・巻き込まれ事故に関する安全教育が十分になされていなかった
- 組織的に安全管理体制ができていなかった
対策
- 点検作業を考慮したうえで機器を設置する
- 作業をする場合は、隣接するエレベーターを停止させてから作業することを徹底する
- 隣接するエレベーターの運転停止や、機器の上の囲いの設置などを盛り込んだ作業手順を作成し、周知する
- 安全管理の役割・責任を明確にするなど体制の見直しを行う
- 作業員に、点検作業中のリスクについて安全教育を実施する。監督者にも、必要な知識・技能についての安全教育を行う
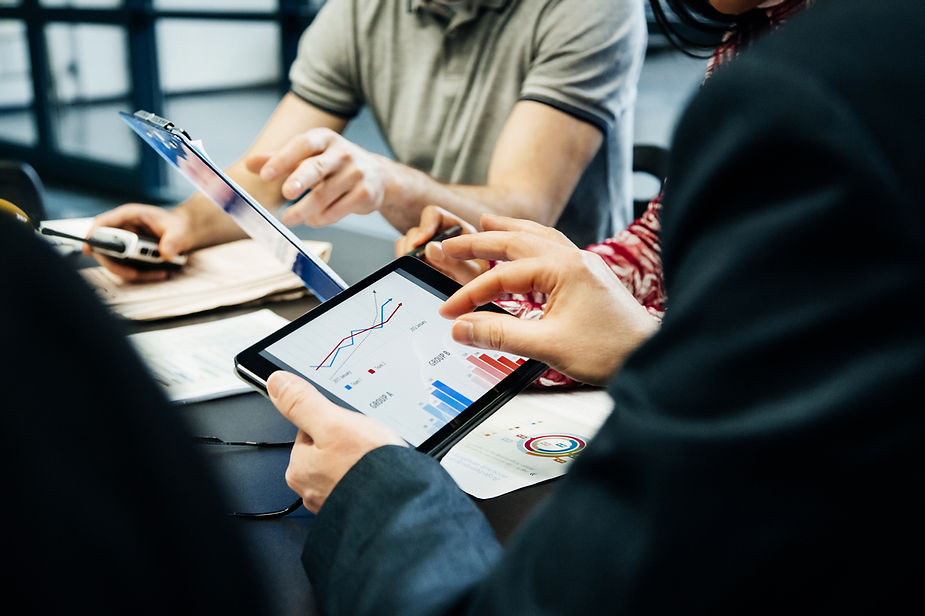
挟まれ事故・巻き込まれ事故の事例を知り、対策を行おう
挟まれ事故・巻き込まれ事故は発生率が高く、死亡する可能性も高い労働災害です。これを防止するためには過去の事例を知り、作業員をはじめ組織全体のリスクに関する意識を高めて、対策を行わなくてはなりません。
過去の事例を見れば、安全な作業標準が作られていなかったり、安全教育が十分になされていなかったり、機器の安全装置が不十分だったりなど、改善することで事故を防げた可能性が高いことがわかります。これらの事例からリスクと原因・対策方法を学び、挟まれ事故・巻き込まれ事故が起きないように対策していきましょう。